Sustainable clothing
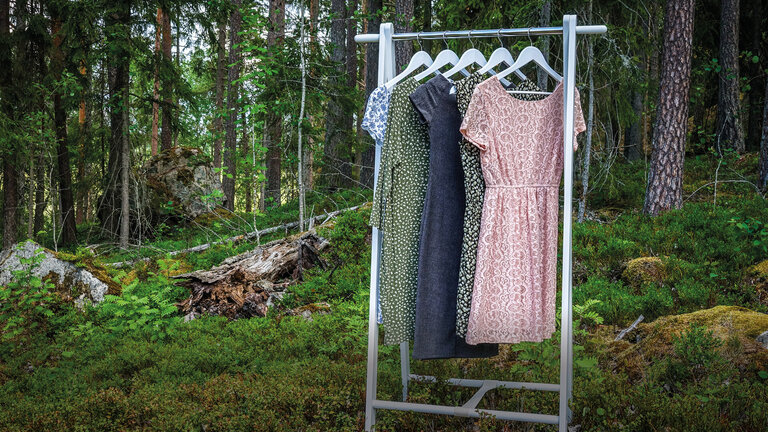
Textile manufacturers, fashion companies and fashion labels are increasingly creating products made of recycled plastic. They include dresses made from old PET bottles, sneakers of recycled sailcloth and even bikinis made from reprocessed fishing nets – anything goes. But consumers are often not aware that not every recycled product helps to protect the climate and rescue the oceans.
About 47 million tons of the annual plastic production in the world comes from the textile industry. According to the Plastic Atlas 2019 (published by the Heinrich Böll Foundation), this puts it in third place for the processing of plastics, behind the packaging industry and the construction sector. So it is not surprising that in today's context, with heated arguments about the climate and a growing awareness of sustainability, many fashion and textile producers place their focus on the care of the environment and recycled products. Some argue in their advertising that clients can help to clean up the oceans by buying clothes made of recycled plastic. Others assure their clients that this will reduce the volume of waste. However recycling plastic from the ocean and making it into clothes does not solve the problem. Even if the plastic is used again, sooner or later it will again become waste, and possibly even find its way into the seas and oceans. So recycling is just an intermediate step which does not reduce the amount of waste. It is just good marketing rather than a sustainable solution.
Recycled with CO2
For one thing, countries like Indonesia and China do not have an adequate infrastructure to collect waste that is sufficiently sorted. Therefore, some manufacturers even fly recycled plastic from Europe to Asia so that it can be processed as yarn and then transported back to Europe. In addition, many plastic products and textiles made of artificial fibers cannot be recycled because they are too heavily contaminated, or not homogeneous. This leads to complicated sorting, cleaning and recycling processes to transform these materials into high quality fibers. In fact, the trend towards recycled plastic is so strong that manufacturers even use completely new PET. This means that either extra plastic is produced for the textile industry, or it is transported by air and thus creates additional CO2. At the end of the day, all of this plastic becomes waste, and the problem of microplastic becomes even greater.
Plastic from the ocean – a black box
PET is a hard and solid packaging material, and it generates a comparatively small amount of microplastic. However if it is reprocessed to create a soft and pliable fiber fabric, for example in fleece, the result is a relatively loose material structure. So every time the garment is washed, up to 140,000 microfibers are flushed into the sewage system, where they become microplastic. Every single wash. Over and over again. And this microplastic is then washed into the sea, into the fish, into our stomachs. And textile fibers recycled from PET also contain antimony trioxide, a catalyst which is carcinogenic and toxic for reproduction systems.
These substances enter the environment during production, recycling – and then finally when the textiles are incinerated. Added to which, the plastic washed up on the shoreline may also contain other attached pollutants which we do not yet know about. Plastic from the ocean is therefore like a black box. Do we really want to wear it on our skin?
The technology has been available for a long time
To ensure that textile products do not pose any risks to human health and the environment, they must be made in an intelligent way so that all of their components can be completely recycled and do not pollute the seas with plastic. This principle is achieved by the Cradle to Cradle® concept, abbreviated as C2C. If a product is manufactured according to the Cradle to Cradle principle, this means that all the substances in the product are healthy and can be reused in a circular production process. Textile manufacturers and fashion labels which base their production on this principle therefore not only have pollution-free sustainable products which later can be separated into homogeneous materials, but they also prevent the creation of waste and the wasteful use of raw materials. In the certification of a product according to the C2C concept, factors such as the use of water and energy and social standards are also examined and optimized by general assessors such as EPEA GmbH – Part of Drees & Sommer.
Garments should also have additional analog or digital keys such as QR codes or fiber markings to show clearly what materials they contain. This could enable the materials to be returned to the appropriate recycling service. For this to work, the fashion labels would need to ask their suppliers to optimize their products so that they are suitable for a circular Cradle to Cradle recycling system – including sewing threads, fabrics and dyes. The necessary technology has been available for a long time. Now, there are also established return and rental systems such as Kilenda, Stay Awhile and MUD jeans.
From jeans and t-shirts to nightwear
Some well-known brands have already successfully tested the C2C concept, and their first fashion lines are already available in the shops. For example, the C&A clothing retailer now offers around 20 variants of T-shirts and jeans that have been certified as Cradle to Cradle enabled products. The food retailer Lidl has developed a recyclable nightwear collection together with experts from EPEA, and this has been sold in its German supermarkets since the fall of 2019. The Austrian company Wolford has applied the C2C principles to the development of biodegradable underwear and technically recyclable legwear. So anyone looking for clothing which will definitely not leave any waste and will protect the environment can already find suitable products today. However, if closed-loop textiles are to become popular in the mass market, other manufacturers – especially large fashion brands – must follow suit.