Sustainable refurbishment in the in the industry branch
Renovating, modernizing, revitalizing - the buildings of tomorrow are already standing: but they need an upgrade! Climate protection, social trends and the adaptation of production lines are changing the requirements for buildings.
REVITALISE EXISTING STOCK - TODAY FOR TOMORROW!
All buildings require regular refurbishment - both technical and energy-related. This is the only way to maintain the value of your property. Because sustainable revitalization makes existing properties fit for the future. What is important here: There are different challenges in every sector and therefore no one-size-fits-all approach! We recognize these and offer you industry-specific refurbishment solutions with our experts.
SUSTAINABLE REFURBISHMENT IN THE INDUSTRIAL SECTOR
Our industry experts know how to make the best possible use of your existing property. They are involved in your revitalization project right from the start, run through various scenarios with you and implement them as required - if desired as a complete package with project management, planning and construction management. We combine an eye for the big picture with expertise down to the smallest detail.
At Drees & Sommer, we combine all the necessary expertise, from energy considerations to building technology and system technology, under one roof. This saves you time, coordination loops with different service providers and costs.
BROWNFIELD - GREENFIELD: WHAT'S BEHIND IT?
In the industry, we differentiate between greenfield, new construction projects on a greenfield site, and brownfield, so-called existing properties that are undergoing renovation.
In the automotive and industrial sectors in particular, there are a number of factors that make it necessary to adapt your existing buildings. One common reason is the modification of production lines. Regardless of whether new production is being integrated or new processes are required: Every change places new demands on existing buildings. Another reason is the adaptation of a building to new energy requirements. These include issues such as the EU taxonomy or digitalization. Many companies are asking themselves questions such as: What is my CO2 footprint at my location and how can I improve it? Do you feel addressed? Then you should make use of our experts' know-how, because we have the answer.
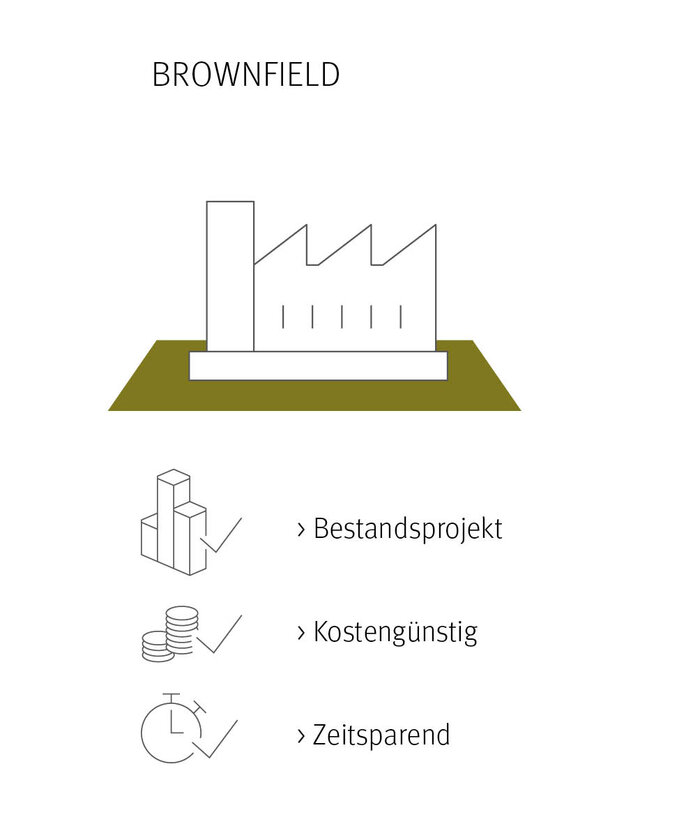
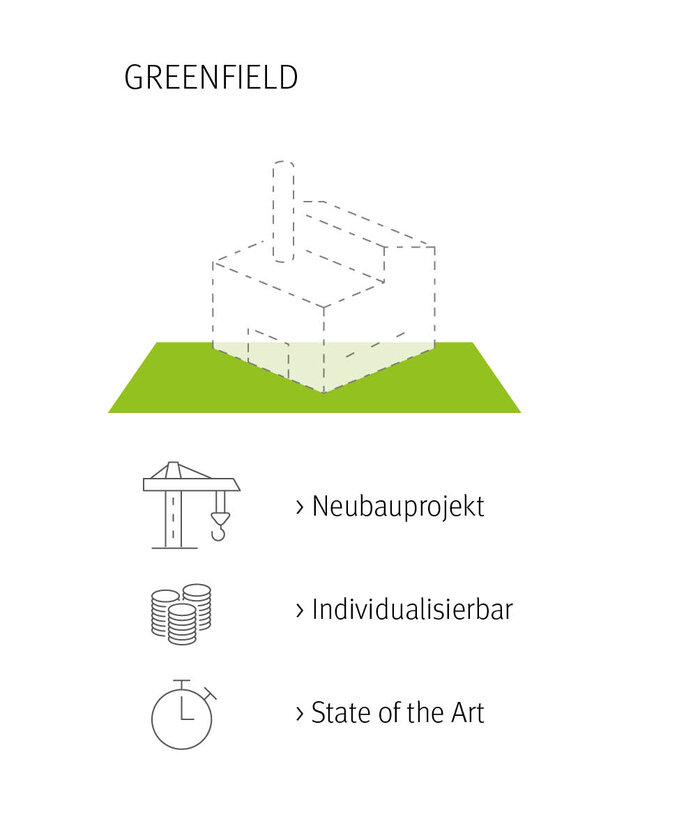
OUR SERVICES
If, for example, you need new approvals for statutory permits, this is referred to as "legislation of existing facilities". Many production sites have been remodeled over the decades. There is a risk here that no utilization or building permit exists. Affected companies must take action and obtain retrospective authorization for the existing building. If they fail to do so, the operating license expires. Often, for example, fire protection is no longer in place or everything no longer complies with the planning permission. We check the existing building for this and restore the legalization.
Other reasons to bring the inventory up to date include shorter product life cycles or changes in the product program. It is also worthwhile for manufacturing companies to take a holistic view of their site and strategically plan sustainable refurbishment measures. Together, we can lead your production to success.
Issues such as the shortage of space affect everyone. When it comes to making an existing brownfield site fit for the future, the charging infrastructure is a standard part of this. Or we can get in from a higher altitude and take a look at spatial planning: What does urban development or neighborhood development look like? And how can we optimally integrate your location into the development?
HOW WE PROCEED
There is no standard procedure. However, we start by looking at your goals and requirements together. As a rule, we focus on your production and ensure that your building provides the right framework for your production processes and fulfils all legal requirements. You also benefit from our expertise in integral factory planning. Integrated factory planning is the optimal symbiosis of production and industrial construction planning. We start the planning process from the product. This ensures that you set new standards with your production. Whether a complete package or individual service modules: We ensure maximum added value. On request, we can integrate CO2 neutrality, Cradle to Cradle® or BIM. Find out more about integral factory planning.